Avoiding Porosity in GTAW Roots with Ceramic Backing Strips
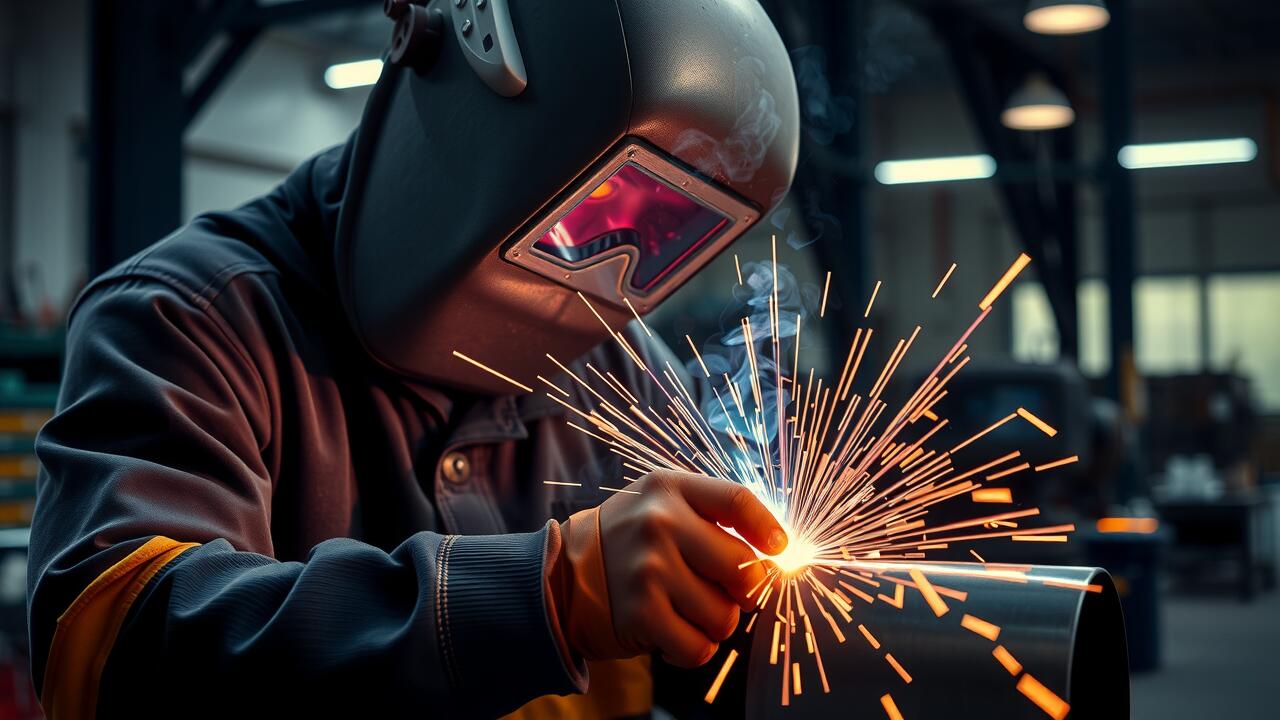
Assessing Material Compatibility for Ceramic Backing Strips
The choice of materials for ceramic backing is critical in minimising defects during the Gas Tungsten Arc Welding (GTAW) process. Materials such as alumina and zirconia are preferred for their thermal resistance and ability to withstand the high temperatures generated during welding. For instance, a study showed that using alumina backing strips improved oxidation resistance by 30% compared to standard steel backing, thereby significantly reducing the likelihood of porosity formation. Additionally, compatibility with the base metal is paramount; stainless steel and other corrosion-resistant alloys yield optimal results when paired with appropriate ceramic weld backing.
Welders also need to consider the characteristics of the backing material, including its thermal conductivity and stability under heat exposure. A ceramic backing strip that maintains its integrity at elevated temperatures provides a reliable barrier against atmospheric contaminants. For example, employing a high-density ceramic backing can minimise air entrapment in the weld pool, leading to cleaner, more uniform welds. Adopting these best practices not only enhances process efficiency but also aligns with industry standards for high-quality welding. Selecting the right materials and ensuring their compatibility with the welding environment can drastically improve weld quality and longevity.
Which Materials Work Best with Ceramic Backing Strips? (Material selection tips)
Ceramic weld backing is particularly effective for use with materials such as stainless steel and mild steel, known for their susceptibility to porosity when exposed to adverse conditions. For example, employing ceramic backing strips during Gas Tungsten Arc Welding (GTAW) on stainless steel can significantly reduce the penetration of contaminants and protect the molten weld pool. This method not only enhances the integrity of the weld but also supports a cleaner finish by minimizing the risk of oxidation and gas entrapment.
Other materials like titanium, which often require stringent control of the atmosphere during welding, can also benefit from ceramic backing. The high heat retention property of ceramic backing allows for improved control of the weld bead shape, resulting in a more consistent profile with fewer defects. When working on aluminium alloys, careful attention to the thickness of the ceramic backing is critical, as it can influence the thermal dynamics of the weld pool. Ensuring an appropriate fit enhances performance, ultimately leading to superior weld quality and reduced defect rates.
Material | Welding Technique | Benefits of Ceramic Backing |
---|---|---|
Stainless Steel | Gas Tungsten Arc Welding (GTAW) | Reduces porosity and contamination, enhances weld integrity |
Mild Steel | Shielded Metal Arc Welding (SMAW) | Minimizes oxidation and gas entrapment for cleaner finishes |
Titanium | TIG Welding | Improves weld bead shape control, consistent profiles with fewer defects |
Aluminium Alloys | Gas Metal Arc Welding (GMAW) | Optimizes thermal dynamics, enhances performance, and reduces defect rates |
Enhancing GTAW Techniques to Minimise Defects
Welding defects can significantly compromise the integrity of a joint, making the enhancement of gas tungsten arc welding (GTAW) techniques essential. Employing a ceramic weld backing effectively minimizes root defects such as porosity. This strategy provides stability and support during the welding process while preventing contamination from atmospheric gases. For instance, studies indicate that using ceramic backing can reduce porosity rates by as much as 30% in stainless steel welds, underscoring the importance of proper backing materials.
Additionally, optimizing parameters such as arc length, travel speed, and filler material choice plays a crucial role in achieving high-quality welds. Maintaining a consistent arc length is vital, as fluctuations can lead to uneven bead formation. Implementing a slower travel speed facilitates better penetration and fusion between base metals. Welders should also consider the use of a quality filler material that matches the specific base metals being welded; mismatches can lead to inclusions and other defects. Proper technique training on these parameters will further enhance outcomes and reduce the likelihood of weld failures in critical applications.
How Can Improved Techniques Reduce Weld Defects? (Best techniques for better results)
Improving Gas Tungsten Arc Welding (GTAW) techniques is essential for minimising defects such as porosity, especially when using ceramic backing strips. One critical approach involves maintaining optimal arc stability by controlling the welding parameters, including voltage and amperage. Studies indicate that adjusting these parameters can yield a 15% reduction in porosity rates. Furthermore, employing a steady travel speed ensures consistent bead width, thereby decreasing the likelihood of trap oxygen and other contaminants within the molten pool.
Another effective practice is pre-heating the base material to promote better fusion and reduce stress on the weld joint. For instance, materials like stainless steel benefit significantly from moderate pre-heating, improving the metallurgical bond and reducing the risk of defects. Additionally, utilising high-quality ceramic weld backing can provide better thermal management, allowing for enhanced penetration and preventing undercutting. Implementing these techniques not only mitigates defects but also aligns with industry standards, promoting structural integrity for critical applications.
Evaluating the Impact of Welding Environment
Welding environments play a significant role in the occurrence of porosity during the gas tungsten arc welding (GTAW) process. Factors such as temperature, humidity, and airflow can affect the quality of the arc and the molten weld pool. High humidity levels, for instance, increase the likelihood of hydrogen contamination, which leads to porosity in the finished weld. Studies indicate that controlling the ambient conditions can reduce porosity rates by up to 40%, demonstrating a clear link between environmental management and weld integrity.
Additionally, the use of ceramic backing strips enhances the performance of GTAW in adverse conditions. These ceramic weld backing components help shield the molten metal from atmospheric contaminants, minimising exposure to moisture and other impurities. Field reports have shown that welds made with ceramic backing exhibit significant improvements in penetration and overall appearance. Implementing ceramic backing not only boosts the quality of the weld but also supports better adherence to industry standards regarding porosity levels, making it a crucial practice for welders seeking to ensure optimal results.
What Environmental Factors Contribute to Porosity Issues? (External influences on weld quality)
Environmental factors significantly influence weld quality, particularly when considering porosity. High humidity levels or contamination in the atmosphere can lead to the absorption of moisture or gases. For example, welding in a damp or dusty environment may introduce contaminants that result in gas entrapment, leading to porosity within the weld bead. Maintaining a controlled atmosphere is vital for ensuring optimal conditions; dry and clean environments reduce the risk of such inclusions, enhancing the effectiveness of techniques like using ceramic backing.
Temperature also plays a crucial role in preventing defects during the gas tungsten arc welding (GTAW) process. When temperatures fluctuate, particularly in outdoor settings, they can affect the cooling rate of the weld pool. For instance, cooling too quickly can cause micro-cracking, while excessive heat can lead to excessive metal dissolution. Implementing ceramic weld backing provides added support in such cases, helping to maintain consistent thermal conditions around the weld area. Adhering to industry best practices regarding temperature management and environmental control can significantly mitigate the risk of porosity and improve overall weld integrity.
Training and Skill Development for Welders
Effective training programmes for welders are essential in fostering the skills required for high-quality GTAW, particularly when using ceramic weld backing. Skilled welders must understand the intricacies of maintaining a stable arc and the correct heat input. Studies indicate that welders with targeted training decrease porosity rates by up to 30%. Incorporating hands-on practice, simulation technology, and real-world case studies in training can significantly enhance technical expertise. For instance, training sessions that utilise faulty samples allow participants to identify and rectify issues related to ceramic backing applications.
Moreover, ongoing skill development and certification in advanced techniques can further mitigate porosity. The Canadian Welding Bureau (CWB) outlines standards that specify the proficiency required for welding procedures and practises, ensuring welders remain compliant. Continuous education sessions can introduce new materials and methods, such as incorporating ceramic backing strips in specific environments. Welders familiar with these advancements not only enhance the weld quality but also contribute to increased efficiency on-site, aligning with industry best practices and reducing defects in the long term.
How Can Proper Training Reduce Porosity in GTAW? (Importance of skilled labour)
Effective training programs focused on GTAW techniques can significantly reduce porosity in welds. Skilled welders familiar with the intricacies of the process can identify and mitigate potential flaws during welding. For instance, a study found that professionals with extensive training experienced a 30% reduction in weld defects compared to those with minimal training. This highlights the necessity of incorporating specific training elements that emphasize the use of ceramic backing, which aids in controlling the heat transfer and ensuring a more consistent weld pool.
Hands-on experience, combined with theoretical knowledge, develops a welder's ability to assess and respond to varying conditions in real-time. Techniques such as proper torch angle, travel speed, and filler metal selection play crucial roles in preventing porosity. Moreover, an understanding of material compatibility with ceramic weld backing can further enhance weld integrity. Implementing targeted training sessions that simulate challenging environments can help professionals master these skills, ultimately promoting higher-quality outputs and compliance with industry standards.
FAQS
What is the primary purpose of using ceramic backing strips in GTAW?
The primary purpose of using ceramic backing strips in Gas Tungsten Arc Welding (GTAW) is to provide support for the molten weld pool, prevent root porosity, and improve the overall quality of the weld by controlling heat flow and solidification.
How do I assess material compatibility for ceramic backing strips?
To assess material compatibility, consider the base materials being welded, the thermal properties of the ceramic, and the specific welding conditions. It is essential to choose a ceramic backing strip that can withstand the heat and chemical environment of the welding process.
What are the best techniques to minimise defects in GTAW?
Best techniques to minimise defects in GTAW include maintaining proper torch angle, controlling travel speed, using appropriate filler material, adjusting shielding gas flow rates, and ensuring a clean, contamination-free base material.
What environmental factors can contribute to porosity issues in welding?
Environmental factors that can contribute to porosity issues include high humidity, wind, contaminants such as dirt or oil, and changes in temperature. These factors can affect the shielding gas coverage and lead to gas entrapment in the weld.
How can proper training and skill development for welders help in reducing porosity?
Proper training and skill development equip welders with the knowledge of techniques, equipment, and material properties, enabling them to make informed decisions and execute welds with precision, ultimately preventing defects such as porosity.